Electroplating - The process
Copper ideally combines the properties of function, design and protection. Due to its excellent thermal and electrical conductivity, copper is used in numerous industrial applications. In decorative chrome plating, copper forms an undercoat that is very easy to polish and therefore serves as a basis for restoring old components. It also improves corrosion protection. Copper plating provides an optional basis for a subsequent nickel-chrome coating.
Advantages of galvanic copper plating
- Good polishability for a high-gloss surface
- Serves as a basis for corrosion protection systems
- Very good electrical and thermal conductivity
- Coated component can be soldered - particularly suitable for electrical contacts
- Wide range of applications from decorative to functional
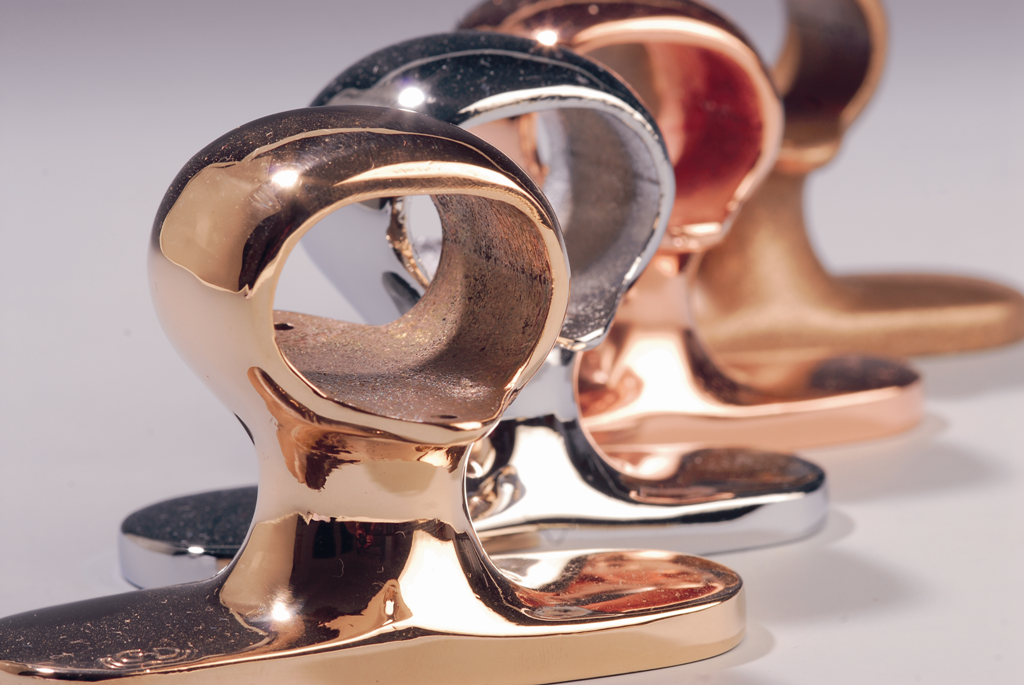
Where is galvanic copper plating used?
Electrical industry
Restoration
Machinery and plant engineering
Are you looking for a partner for copper plating?
Then contact us now.
We look forward to being able to process your request individually.
Technical specifications
Materials: | Steel, brass, copper, bronze, stainless steel |
Plant capacity: | 500 x 300 x 150 mm (oversize by arrangement) |
System technology: | Frame, drum |
Production guidelines: | RoHS, REACH, 2000/53/EC (end-of-life vehicles) |
Execution | high gloss, glossy, matt |
Layer thickness | usually 15 - 20 µm |
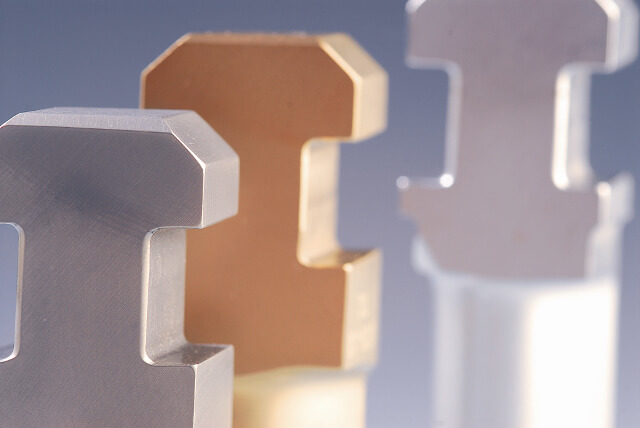
Why choose TECHNO-COAT?
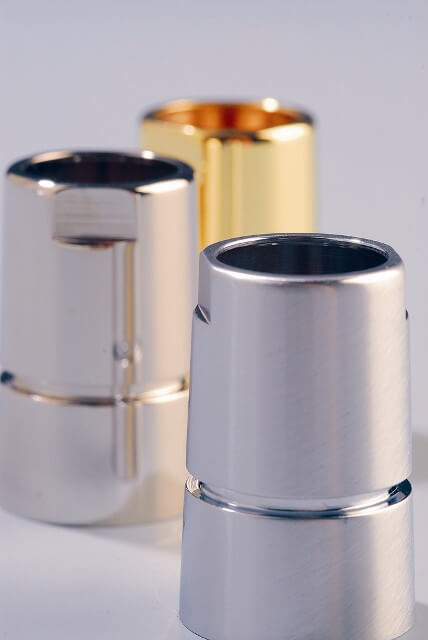
Everything from a single source
Copper is used as a base or intermediate layer in many coating systems. We also offer you numerous supplementary processes.
Speed
Thanks to smooth coating processes, flexibility and large capacities, you will receive your copper-plated products in record time.
Many years of experience
More than 25 years of know-how in the field of surface finishing also flow into the electroplating of your products.
High quality standards
Quality is one of our highest company values. Through internal testing procedures and our certified quality management, we live up to this claim every day anew.
How we copperplate - the process
1
Pre-treatment
Depending on the delivery condition, pre-treatment may be necessary to remove unwanted contamination or residues from previous processes. For this purpose, the parts are processed in an ultrasonic cleaning system.
2
Decoction degreasing
A further cleaning step takes place in the boil-off degreasing process. This removes the last residues that may not have been removed during ultrasonic cleaning.
3
Cascade sink
The chemical residues of the degreasing/cleaning process are neutralized. This step is repeated during the process.
4
Pickling
The metal surface is freed from existing corrosion. Various additives ensure that the base material is largely unaffected.
5
Electrolytic degreasing
Electrolysis creates small bubbles on the surface. These cause fine cleaning by blasting off dirt particles.
6
Activation
This process step removes existing passive layers and activates the surface for the subsequent coating.
7
Copper plating
Pure copper is brought into solution by electrolysis and deposited as a copper layer on the component to be coated by excess electrons via an aqueous phase.
8
Combination layer
After copper plating, either further electroplating, e.g. nickel-chrome, or mechanical processing, e.g. polishing, can be carried out directly to achieve a higher degree of gloss.
9
Drying
The copper-plated product is dried with hot air in the circulating air dryer.
Frequently asked questions
What are the advantages of copper plating?
The copper plating of metallic components has the following advantages:
- Well suited as a base or intermediate layer
- Can be polished to a high gloss
- Ideal basic protection against corrosion
- Electrically conductive
- thermally conductive
- Solderable
- Good shrinkage properties
- creates a diffusion barrier
What are the disadvantages of copper plating?
The following disadvantages can occur with copper-plated components:
As copper is not stable in the atmosphere, it tends to discolor or tarnish if it is not protected by a coating.
Which materials can be copper-plated?
Brass is mainly copper-plated directly, while steel is given a thin undercoat of nickel.
What investment capacities are available?
Our system capacity is 500 x 300 x 150 mm. For larger components, please contact us directly.
Which system technology is used for copper plating?
Various racks and a drum for bulk material are available for copper plating.
Which manufacturing guidelines are adhered to?
We adhere to the following guidelines when coating with copper:
- RoHS
- REACH
- 2000/53/EC (end-of-life vehicles)
Request now
Send us your request simply and conveniently using the form. You will receive our information on the coating process directly afterwards. If you are not sure about certain details, please contact us directly by e-mail or telephone or leave the fields blank.
We look forward to receiving your inquiry!
Your contact person
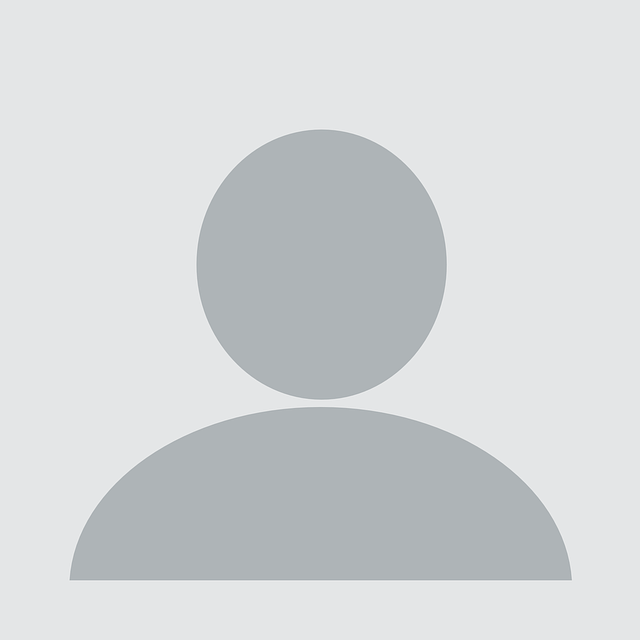
- Reiko Röthig
- r.roethig@techno-coat.com
- +49 (0) 3583 / 77 21 - 34